With the global shift toward renewable energy and a low-carbon lifestyle, home energy storage systems have become essential for modern households. According to market reports, the demand for these batteries is expected to grow at an annual rate of over 20% by 2030. This surge reflects their ability to store solar energy, reduce electricity costs, and provide reliable backup power.
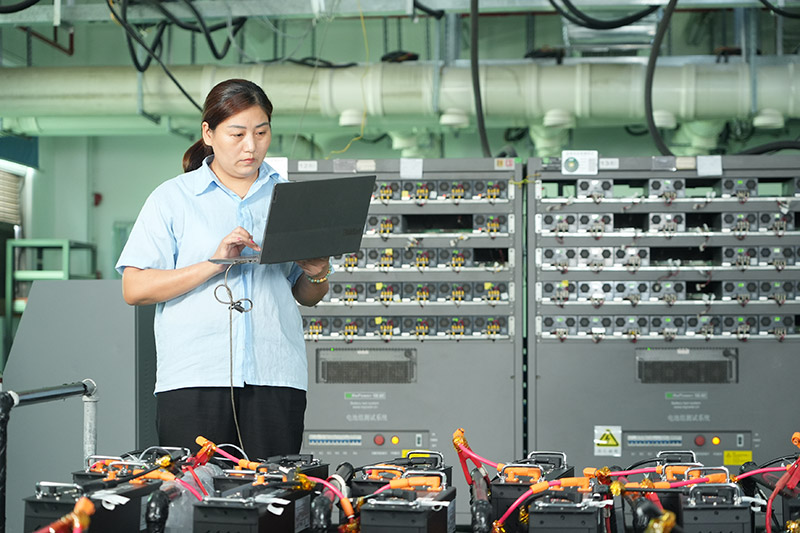
However, many people remain unaware of how these batteries are made. Understanding the production process can help consumers appreciate the quality and engineering behind these systems, aiding in informed decision-making. In this article, we’ll take a closer look at the manufacturing steps, highlighting the precision and technology required to produce high-quality residential energy storage batteries.
Step 1. Raw Material Procurement and Inspection
The first step in producing high-quality home energy storage batteries is sourcing premium raw materials. Key components include:
- Electrode materials: Lithium-ion batteries use cathode materials like lithium iron phosphate (LFP) and anode materials like graphite.
- Electrolytes: Critical for lithium-ion conduction within the battery.
- Separators and casings: Ensure safety and structural integrity.
Once the materials arrive at the facility, they undergo rigorous quality inspections. Only materials that meet strict specifications proceed to the next stage. This step is crucial because material quality significantly influences battery performance and durability.
Step 2. Electrode Sheet Manufacturing
This process involves several critical steps:
- Coating: Active materials are uniformly coated onto metal foils to create cathode and anode sheets.
- Drying: The coated sheets are dried in high-temperature environments to remove excess solvents.
- Calendering: The dried sheets are compressed under high pressure to increase material density and enhance energy efficiency.
These steps require precision machinery and strict quality control to ensure uniformity and performance consistency.
Step 3. Battery Assembly
In this stage, the battery’s core components are combined. Key steps include:
- Cutting and stacking: Electrodes are cut to size and stacked or wound to form cells.
- Electrolyte filling: Electrolytes are injected into the cells to enable ion transfer.
- Sealing: Cells are sealed using aluminum-plastic films or metal casings to protect against external contaminants.
The assembly process typically occurs in a cleanroom environment to minimize the risk of dust or impurities affecting the battery’s operation.
Step 4. Formation and Grading
This phase activates the battery cells and assesses their performance:
- Formation: Cells undergo controlled charge and discharge cycles to stabilize electrode materials.
- Grading: Each cell is tested for capacity, internal resistance, and voltage to identify high-performing units.
This step ensures that only the best cells are used in the final product, maintaining high-quality standards.
Step 5. Module and System Integration
Individual cells are grouped to create battery modules, which are integrated into complete energy storage systems. The process involves:
- Cell arrangement: Cells are arranged based on system design requirements.
- Welding and connection: Cells are connected using wires and terminals.
- BMS Installation: A Battery Management System (BMS) is added to monitor and protect the battery.
The completed modules may also be integrated with inverters, chargers, and other components to form a functional energy storage unit.
Step 6. Performance and Safety Testing
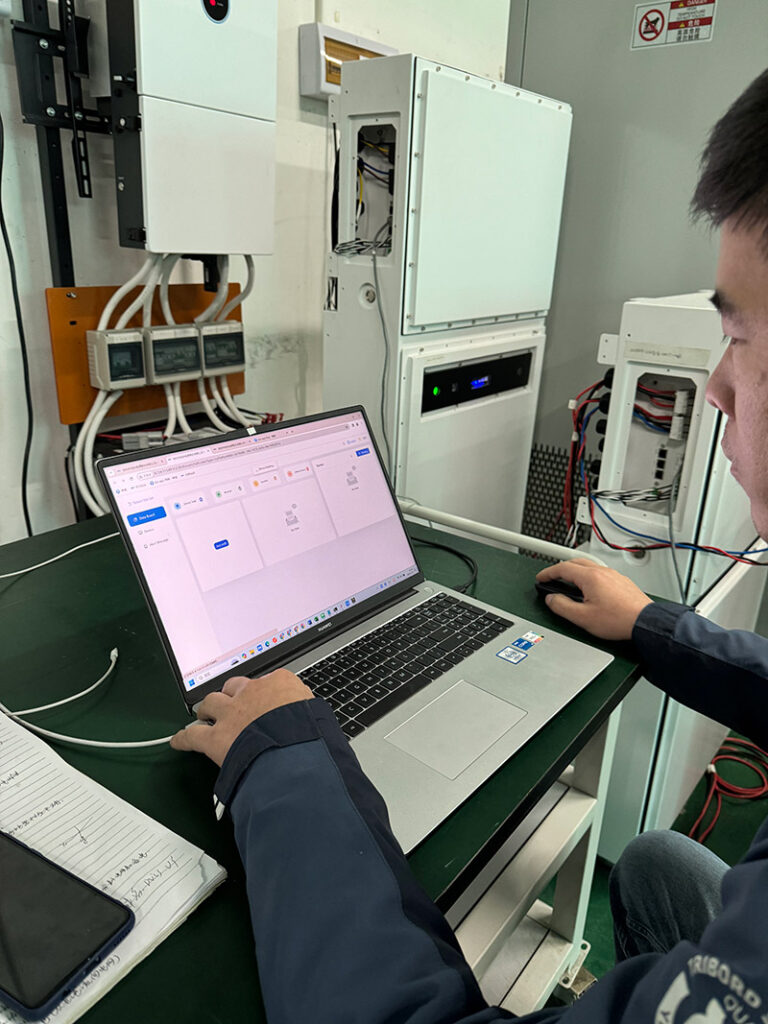
Each energy storage system undergoes comprehensive testing to ensure reliability:
- Electrical testing: Confirms capacity, cycle life, and energy efficiency.
- Environmental testing: Simulates extreme conditions such as high/low temperatures and humidity changes.
- Safety testing: Includes overcharging, short circuits, and pressure tests to ensure the battery’s resilience against failures.
Testing data provides a clear certification of the product’s quality and safety.
Step 7. Packaging and Shipment
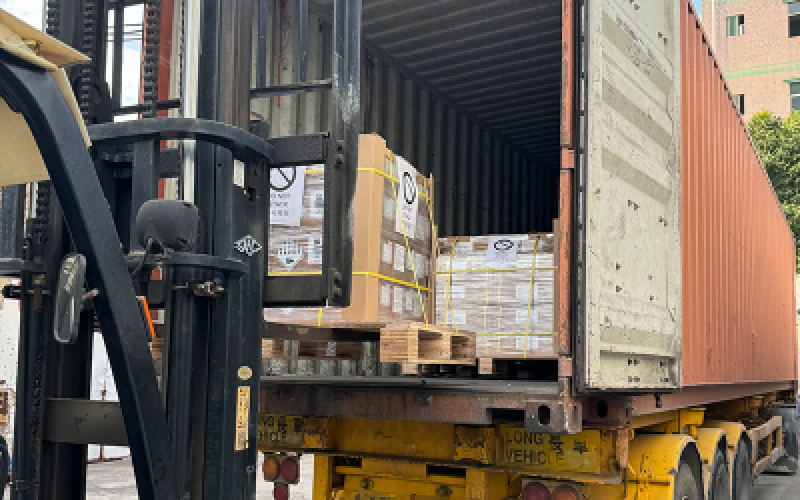
Once tested, batteries are carefully packaged to prevent damage during transportation. Packages include compliance certifications and user manuals. Using efficient logistics networks, the products are quickly delivered to customers worldwide.
Conclusion
The production of home energy storage batteries involves multiple meticulous steps, from raw material inspection to rigorous safety testing. Each stage relies on precision equipment, advanced technologies, and strict quality controls to produce reliable and efficient products.
As automation and advanced manufacturing technologies evolve, production efficiency and product quality will continue to improve. Understanding these processes enables consumers to make informed decisions and choose the best energy storage solutions.
Stay tuned for more insights on home energy storage batteries and related technologies!
FAQs About Home Energy Storage Battery Production
- What materials are used in home energy storage batteries?
Core materials include lithium iron phosphate (LFP) for cathodes, graphite for anodes, electrolytes, separators, and casings. - How long does it take to produce a battery?
The process typically takes 3–5 weeks, depending on the production scale, from raw material procurement to final testing. - What is the most critical step in production?
Quality control during raw material inspection and cell formation are crucial to ensure performance and safety. - How are batteries tested for safety?
Safety tests simulate conditions like overcharging, short circuits, and high pressure to ensure reliability under extreme scenarios. - How does automation affect production?
Automation improves precision, reduces production times, and enhances overall quality, making batteries more affordable and efficient.