Introduction: What do you need in a good quality lithium battery factory?
In today’s rapid growth of new energy demand, lithium batteries have become a key product to achieve green energy and low-carbon life. The production of high-quality, long-life lithium batteries requires advanced production technology and a perfect quality management system. In addition, intelligent management, environmentally friendly production, and a professional R&D team are also key to ensuring the production of high-quality lithium batteries.
BST, a lithium battery manufacturer with 22 years of experience, has developed a set of efficient and precise production processes through its rich industry experience and automated production equipment. From electrode manufacturing, liquid injection, and encapsulation to aging and testing, each step is strictly controlled to ensure that the energy density, cycle performance, and safety of the battery meet high standards. The following is an analysis of the fully automated lithium battery production process.

**1. Electrode Manufacturing Process: Mixing, Coating & Calendering
Electrode manufacturing is the starting point of lithium battery production, and also the core step that determines the battery performance. Through sophisticated automated equipment, the factory is able to ensure the standardization of each step of the operation to achieve high energy density and long life of the battery.
- Mixing: Precise proportioning and mixing of cathode materials (e.g. lithium iron phosphate or ternary materials), anode materials (e.g. graphite), conductive agents, and binders into a slurry.
- Automation Highlights*: The automated mixing system ensures uniform mixing of each batch of materials and reduces errors.
- Coating: Positive and negative electrode slurry is evenly coated on aluminum and copper foils to ensure uniform coating.
- Automation Highlight*: Double-sided synchronous coating equipment monitors the thickness in real-time, making the coating more stable.
- Drying & Calendering: Drying the electrodes in a dust-free environment and then calendering them makes the density of the electrodes higher and ensures the energy density and consistency of the battery.

**2. Electrode cutting and winding/stacking process
- Cutting: Cut the dried pole piece into a specified size to avoid rough edges and ensure close bonding with the diaphragm.
- Automation highlights: Laser-cutting technology reduces waste and makes neat cuts.
- Winding/Stacking: Combine the positive electrode, negative electrode, and diaphragm in the form of winding or stacking according to the battery design.
- Winding process: Suitable for cylindrical and flexible pack batteries. The electrode and diaphragm are tightly wound together.
- Stacking process: Suitable for square batteries, more suitable for large-capacity energy storage products.
- Automation highlights: Fully automatic winding machine and stacking machine precisely control each step of operation, with small errors and high efficiency.

**3. Cell assembly: Liquid injection and encapsulation
- Liquid injection: In a dry room, electrolyte is injected into the cell to ensure the ionic conductivity of the battery.
- Automation Highlights: High high-precision automatic liquid injection system reduces electrolyte waste and ensures uniform injection.
- Encapsulation: The liquid-injected cells are heat-sealed to prevent electrolyte leakage.


**4. Synthesis and Dispersion: Activate battery performance
- Chemical Formation: The battery is first charged and discharged under a specific environment so that the electrode material reacts with the electrolyte to generate a stable SEI film and enhance battery life.
- Automation Highlight: An intelligent chemical formation system monitors the battery voltage and temperature to ensure a stable process.
- Capacity Separation: The capacity test of the batteries that have been chemically formed is graded by capacity to ensure product consistency.


**5. Assembly and testing: protection system and performance calibration
- Battery assembly: assembling the cells into the battery casing, integrating protection circuits and battery management system (BMS) to enhance the safety and management of the battery.
- Aging Test: Conducts a long aging test on the battery to detect its long-term performance stability.
- Automation highlights: The aging test system is equipped with a data acquisition module to monitor battery capacity changes in real-time.
- Final Inspection: The fully automated inspection system conducts an all-around inspection of the battery’s voltage, internal resistance, capacity, and safety to ensure the high quality of the batteries leaving the factory.
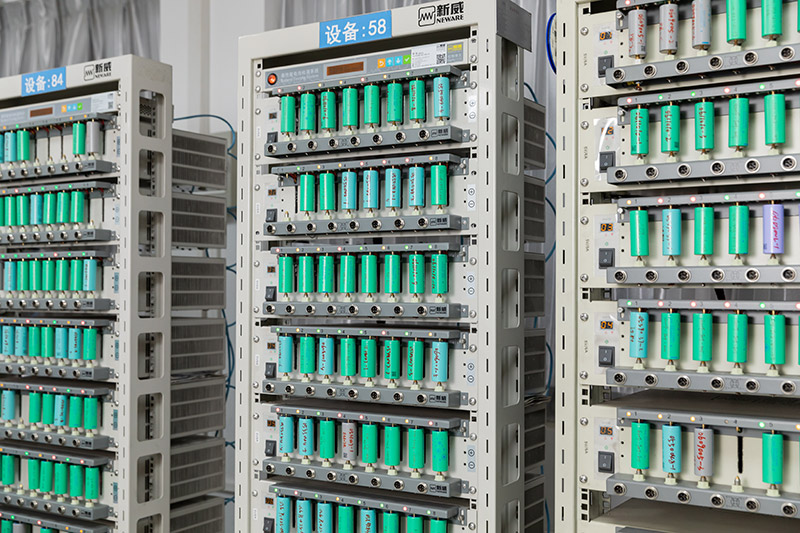
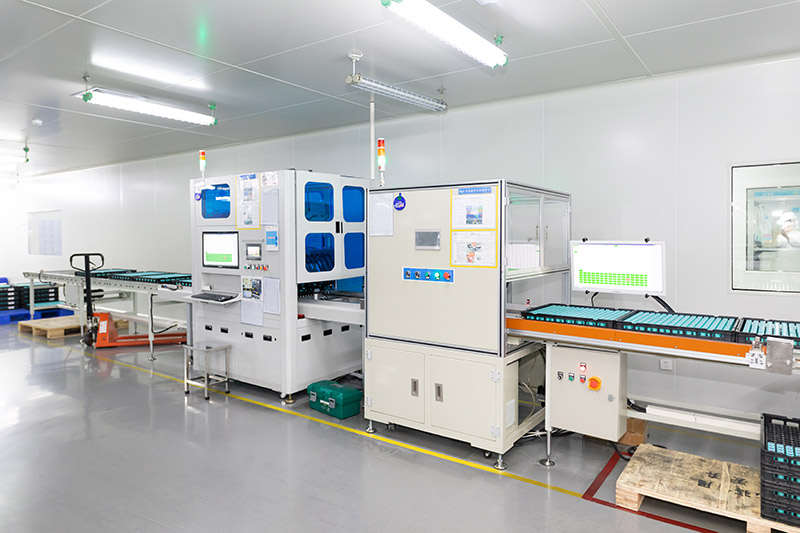
**6. Packaging and Ex-factory: Ensure the delivery quality
Through the labeling, packaging, and traceability system, every battery leaving the factory can be traced back to the production process. After qualified batteries are packed, they will enter the warehouse and wait for shipment.


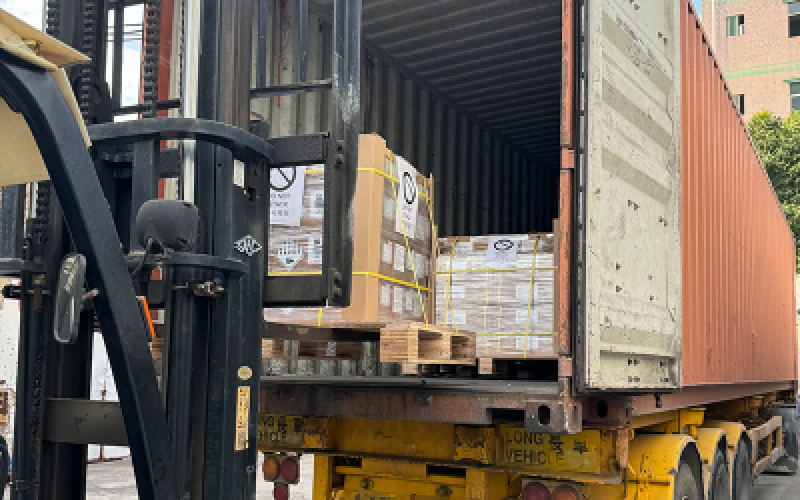
Conclusion: Core Elements of Efficient Li-ion Battery Production and New Energy Future Trends
A high-quality lithium battery production process cannot be separated from the support of fully automated equipment and also relies on an intelligent management system and a strict quality control system.BST ensures the high quality and stability of each battery through a comprehensive set of automated production processes and data monitoring systems. From mixing and coating to encapsulation and aging testing, the application of intelligent technology reduces human error and improves production efficiency and product consistency.
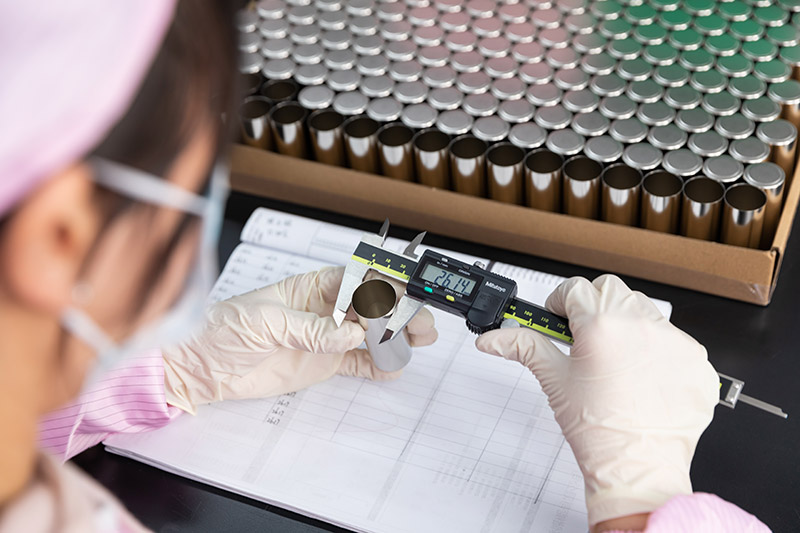
The four major elements of high-efficiency lithium battery production
- Intelligent management: automated equipment with big data monitoring to reduce errors and improve efficiency.
- Environmentally friendly production: Reduce waste and pollution through more environmentally friendly production methods.
- R&D Innovation: Continuously innovate technology to improve battery energy density and cycle life.
- Perfect after-sales service: Provide professional after-sales service to ensure customers’ worry-free use.
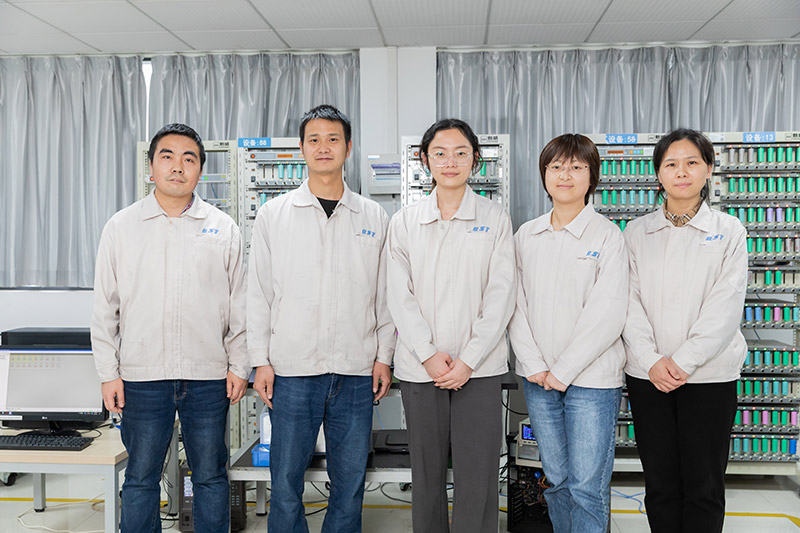
Future Trend: Bright Prospect of New Energy Industry
With the rapid growth of global demand for renewable energy, lithium batteries, as a support for new energy, will maintain a high rate of development in the coming years. Its application areas have expanded from household energy storage and industrial energy storage to electric vehicles, and several industries are accelerating the application of clean energy.
In the future, the new energy market may show the following trends:
- Higher energy density and longer service life: technological advances will enable batteries to continue to increase their energy density and further extend their service life.
- Environmental protection and sustainable development: Strengthening of environmental regulations has led to greener and more sustainable production and recycling of lithium batteries.
- Diversification of energy storage technologies: New technologies such as hydrogen and solid-state batteries are emerging, bringing more options to the energy storage market.
- Global Low Carbon Goal: The promotion of the carbon neutrality goal will bring the continuous growth of lithium battery demand, and the energy storage industry will usher in a new round of development peak.
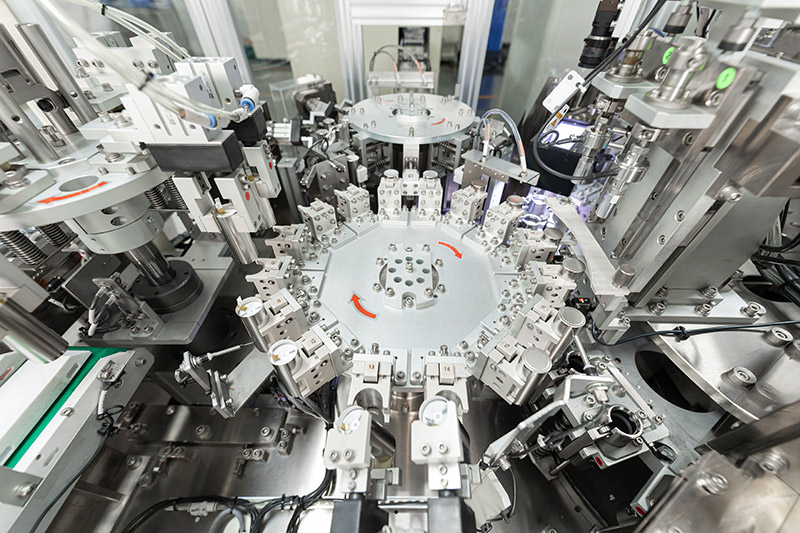
BST will continue to lead the innovation of green energy storage technology, provide reliable lithium battery solutions to global customers through efficient production processes, help the world realize the goal of low-carbon life, and jointly promote a sustainable new energy future.